Frequently Asked Questions
Background | Contact Information | What is Being Remediated | Project Schedule | Health & Safety | Project Oversight | Dust, Noise, Odors | Access & Truck Traffic | Site Restoration | Updating Employees & the Community
BACKGROUND
Q. What was a Manufactured Gas Plant (MGP)?
A. Prior to the widespread availability of natural gas, gas was “manufactured” through a process of heating coal in specialized ovens. These facilities, called Manufactured Gas Plants (MGP), were common in many urban areas of the United States during the late nineteenth and early twentieth centuries.
Manufactured gas was used for residential and street lighting and cooking. The manufactured gas process produced by-products, such as coal tar and other chemicals that were also used in the chemical, dye and pharmaceutical industries. An unintended consequence of the MGP industry was the effects from coal tar and various by-products on the environment.
Q. Who is responsible for the remediation of the site?
A. PSE&G is the responsible party. Although the property is currently owned by the State of New Jersey, PSE&G is responsible for the site’s remediation. The NJDEP Site Remediation Program Interest (PI) number for the Site is G000005462 and the Activity #: LSRI120001.
Q. Has PSE&G completed a remediation project for a former MGP site of similar size?
A. Yes. PSE&G has a total of 38 MGP sites throughout New Jersey and to date has successfully remediated 27 MGP sites. The other 11 sites are in various stages of completion. This work is required by NJDEP.
An estimated 100,000 tons of soil are planned for removal from the John Fitch Way Project. PSE&G has successfully completed many projects of similar and larger size over the last 20+ years. Most recently, contractors for PSE&G successfully removed approximately 300,000 tons of soil as part of its Harrison former MGP remediation project, which was completed in 2022.
Q. Why is this project necessary and why does it have to be done now?
A. PSE&G is committed to addressing the legacy impacts of its former Manufactured Gas Plant (MGP) sites in accordance with the New Jersey Department of Environmental Protection’s Technical Requirements for Site Remediation. PSE&G has been working since the early 2000s to investigate and plan for this site’s remediation. PSE&G has worked for more than 10 years to secure an agreement with the State of New Jersey to allow us to meet these obligations. We greatly appreciate the current Administration’s support.
CONTACT INFORMATION
Q. Who do I contact if I have a question or concern?
A. PSE&G is committed to open communication with state employees, community leaders, residents, and businesses. We encourage the community to contact us with questions or concerns.
- Call the Project Information Line: (855) 356-2383* (TTY callers please use 711)
- Email us: comments@jfitchwayproject.com (right click to copy link into your email)
* Please note the Project Information Line is automated. You will be prompted to leave your name, contact information and the reason for your call. One of PSE&G’s community liaisons will return your call as soon as possible.
WHAT IS BEING REMEDIATED
Q. What are the contaminants driving the remediation?
A. The remediation is driven by the presence of MGP coal tar and oil by-products in the soil and groundwater that include benzene, polycyclic aromatic hydrocarbons (or PAHs) and metals. Accordingly, the soil containing these by-products and compounds will be excavated and trucked to licensed off-site soil treatment facilities. The remedial site will be restored with clean fill and capped with asphalt. Groundwater encountered during soil remediation activities will be treated and conveyed off-site in accordance with applicable federal and state regulations and permits.
Q. What is the extent of impacts to be remediated?
A. The remediation site is a portion of the three-acre, State-owned property on the corner of South Warren Street and Market Street (Block 10701, Lots 1, 2 and 3). The property is currently composed of a large parking lot, an above ground water tank and a helicopter pad near the New Jersey Department of Labor and Division of Taxation buildings.
PSE&G plans to excavate approximately 100,000 tons of MGP-impacted soil. Any infrastructure related to the former MGP operations that remain underground also will be removed. Most of the work will be performed within a temporary sprung structure (i.e., a tented enclosure). Excavated soil will be trucked to a licensed off-site facility for treatment and beneficial reuse as landfill cover. The remedial site will be restored with clean fill and capped with asphalt. Groundwater encountered during soil remediation activities will be treated and conveyed off site in accordance with permitting.
The removal of impacted soil will also have a beneficial effect on groundwater, which will continue to be monitored following the soil remediation. The City of Trenton water supply is not impacted.
Q. Will you need to address soil impacted by the MGP contaminants on other parts of the property in the future?
A. No. PSE&G has conducted several investigations of the property to determine the extent of impacts – both horizontally and vertically – by the MGP contaminants to soil. The results of these activities were documented in a Soil Remedial Investigation Report (RIR) submitted to the NJDEP in November 2006. The upcoming soil remediation project will address all soil impacted by the MGP contaminants and there will not be a need for further or future soil remediation on any other parts of the property.
PROJECT SCHEDULE
Q. How long will the work take to complete?
A. The work is anticipated to take approximately 18 months to complete from the April 15, 2024 mobilization date.
Q. What are the working hours for the site?
A. The working hours for the site are 7 am to 6 pm, which are the hours permissible by the city.
Q. The site has been investigated since 2000, why has it taken until now to remediate?
A. Several factors have contributed to the remediation timeframe. They include:
- Most importantly, the fact the site as it existed did not pose a risk to human health. Therefore, health risk to occupants was never a driver to initiate the remediation;
- There were and are significant logistical challenges associated with a remediation of this size and complexity that required extended time to evaluate and plan for;
- Following the completion of the investigation and delineation of the contamination, various remedies were evaluated. The Remedial Action Workplan for excavation was ultimately approved by the NJDEP in 2011;
- The remediation was anticipated to start in 2014. However, due to logistical challenges and changes in State administration, it was decided to delay the project for 18 to 24 months;
- In 2009, New Jersey Legislature passed the Site Remediation Reform Act and set forth sweeping changes to the way in which sites are remediated in New Jersey. Responsible parties were required to hire a Licensed Site Remediation Professional (LSRP). LSRPs “step into the shoes” of the NJDEP to oversee the remediation of contaminated sites. As part of this legislation, Regulatory and Mandatory remedial timeframes were established by the NJDEP; and
- Securing a negotiated agreement with the Administration because the property is owned by the State of New Jersey. Negotiations began prior to the current Administration. These negotiations were ultimately finalized in 2023, at which time expedited planning, engineering and contracting for the upcoming remediation was initiated.
HEALTH & SAFETY
Q. Is there a public health concern?
A. Potential concerns from MGP contaminants are associated with ingestion (eating) of the affected soil or drinking the affected groundwater. The City of Trenton water supply is not impacted, and the buildings, streets and sidewalks served as an effective barrier to ingestion. The public health is of utmost concern to PSE&G and the State of New Jersey as the property owner. During the remediation, PSE&G will implement a safety plan, including air monitoring.
Q. What is the air monitoring early warning system?
A. To be protective of public health and safety, PSE&G had a third party develop a site-specific Perimeter Air Monitoring Plan (PAMP).
The purpose of perimeter air monitoring is to measure potential airborne emissions of volatile organic compounds (VOCs), polycyclic aromatic hydrocarbons (PAHs), and dust. These measurements are compared to alarm conditions and action levels. The alarm levels serve as an early indicator to take action to ensure levels at the site perimeter do not exceed the health-based levels consistent with EPA guidance.
If total volatile organic compound (VOC) or dust levels reach the threshold, an “alarm” is triggered to alert the dedicated air monitoring technician of the condition. The technician then follows established protocols of notification to the contractor and health and safety officer to ensure additional actions are taken to reduce levels. These actions may be the application of additional foams or other vapor suppressants, utilizing water, adding clean soil to serve as a temporary cover, or work stoppage if necessary.
This very conservative approach ensures levels at the site perimeter remain below the site-specific chronic action levels.
Q. If an air monitoring alarm goes off will employees be notified and evacuated?
A. There is no scenario related to vapor or dust levels that would warrant an evacuation of the building.
If total volatile organic compound (VOC) vapor or dust levels reach the threshold set by the PAMP, an “alarm” is triggered and the dedicated air monitoring technician is alerted to the condition. The technician then follows established protocols of notification to the contractor and health and safety officer to ensure additional actions are taken to reduce levels. These actions may be the application of additional foams or other vapor suppressants, adding clean soil to serve as a temporary cover, or work stoppage if necessary.
Q. Will air monitoring data be made public?
A. Yes. The data from the weekly confirmatory samples will be placed on the project website’s Air Monitoring page.
Q. Is there a potential for an explosion from the contaminants?
A. No. Concentrations of the contaminants are at low environmental levels. There is no fire or explosion risk related to the contaminants.
Q. Is a third party conducting the air monitoring?
A. Yes. PS&S is conducting the air monitoring. The Perimeter Air Monitoring Plan that PS&S is implementing was developed by Triumvirate Environmental.
Q. How frequently is the monitoring system being tested for accuracy and recalibrated?
A. Daily. The system is tested for accuracy and recalibrated each morning before soil disturbance work begins.
Q. How can I find out more about the studies that are the basis of the air monitoring approach?
A. The health-based action levels in the Perimeter Air Monitoring Plan were derived for the John Fitch Way Project using the EPA “Regional Screening Levels (RSLs) for Chemical Contaminants at Superfund Sites.” The approach has a RSL calculator that produces risk-based screening levels based on inhalation toxicity factors. The basis for the EPA toxicity factors is provided in the calculator. Here is a link to learn more (https://epa-prgs.ornl.gov/cgi-bin/chemicals/csl_search).
For example, the source of benzene inhalation toxicity factors is EPA’s Integrated Information System (IRIS) and the EPA’s IRIS risk assessments for benzene can be located at https://iris.epa.gov/AtoZ/?list_type=alpha. The IRIS benzene human health assessment provides a characterization of the risk to humans from inhalation exposure to benzene and references for key relevant scientific studies.
Q. How often will the perimeter of the temporary enclosure be checked to ensure it is intact?
A. The temporary enclosure will be inspected daily to ensure the integrity of the enclosure and negative pressure conditions necessary for maintaining air quality within the enclosure is properly maintained.
Q. What are your plans to communicate to employees if there is an emergency on the project site?
A. PSE&G will notify State representatives of any emergency resulting in the need to call the City of Trenton’s Emergency Services.
In accordance with the project’s Health and Safety Plan (HASP), PSE&G also will notify State representatives of any situation at the project site that results in a permanent stop work order.
Additionally, PSE&G will notify State representatives at its weekly status meetings if a temporary stop work order occurred the prior week. As safety is PSE&G’s first priority, a temporary stop work order can be made in relation to any onsite concern or potential risk related to worker safety. This will include if the internal “early warning threshold” level for air monitoring was exceeded and a temporary stop work order was enacted to ensure the perimeter action level was not exceeded.
Q. Will air be regularly monitored throughout the day as work is being conducted?
A. Yes. Monitoring of air within the enclosure and ambient air on all sides of the enclosure will be monitored continuously while soil disturbance work is performed.
Q. Should there be additional concerns for employees with pre-existing health conditions?
A. If you have concerns regarding your personal health, you should consult your doctor.
The potential hazard associated with MGP-related materials involves ingestion of impacted soil or impacted groundwater. Groundwater is not a source of drinking water for the area.
To protect air quality at and around the site while excavation is performed, PSE&G hired a third-party toxicologist to develop a Perimeter Air Monitoring Plan (PAMP) specific to the site’s conditions.
To learn more about the PAMP, visit the Air Monitoring Page.
Q. Has the project team taken the wind conditions on campus into account in relation to air monitoring?
A. Yes. Wind conditions and prominent wind direction were and will continue to be considered in the development of the Perimeter Air Monitoring Plan. Additionally, a meteorological or MET station to track wind conditions will be in place for the duration of the remediation as part of the air monitoring program.
Q. How often are the tracking pads cleaned of the contaminated soil?
A. The tracking pads will be inspected on a daily basis. The tracking pads will be refreshed or cleaned if any contaminated soil is observable at the top of the washed/ crushed stone. Typically, some type of restoration or cleanup of the tracking pads is conducted once per month.
PROJECT OVERSIGHT
Q. Is NJDEP supervising the work?
A. In 2012, NJDEP fully implemented the Licensed Site Remediation Professional (LSRP) program. In New Jersey, LSRPs are responsible for providing guidance and oversight to ensure remediation projects are performed in accordance with state regulations. The LSRP for this site is Michael Newton.
The work plan for the site remediation was reviewed and approved by the LSRP and then submitted to NJDEP, which provided no comments. After each phase of work is completed, PSE&G will develop a report documenting its actions. The report will be reviewed and approved by the LSRP and submitted to the NJDEP.
DUST, NOISE, ODORS
Q. Will there be noise?
A. The work performed will create sounds like that of a typical construction site. Truck safety back up alarms, other equipment and workers voices will be heard beyond the site perimeter.
Q. Will you provide the MSDS sheets for the odor suppressants that will be used on site?
A. Yes. The Safety Data Sheets can be found here:
Q. Can the odors or suppressant foam trigger symptoms in employees with respiratory conditions?
A. Any person with a known respiratory condition should consult their doctor on what their personal triggers may be and what actions they can take to eliminate or reduce such triggers.
PSE&G can minimize the potential for people not working on the project to exposure to odors and any of materials we use to do our job, including the odor suppressant foams that we use. To that end, PSE&G has chosen to conduct this remediation beneath an enclosure or sprung structure. This structure will help to minimize odors and the likelihood that use of odor suppressant foams will be blown beyond the site perimeter.
Q. What will be the procedure for reporting issues related to odor and dust?
A. Call the Project Information Line at (855) 356-2383 or email the project at comments@jfitchwayproject.com. A PSE&G representative will respond to your call or email and take the necessary steps to notify the project site of the concern. PSE&G also will notify the designated project contacts at Treasury of any call or email of this nature.
ACCESS AND TRUCK TRAFFIC
Q. Will any of the state parking lot entrances be closed?
A. Yes. Access to the site where the soil remediation is being performed will be closed.
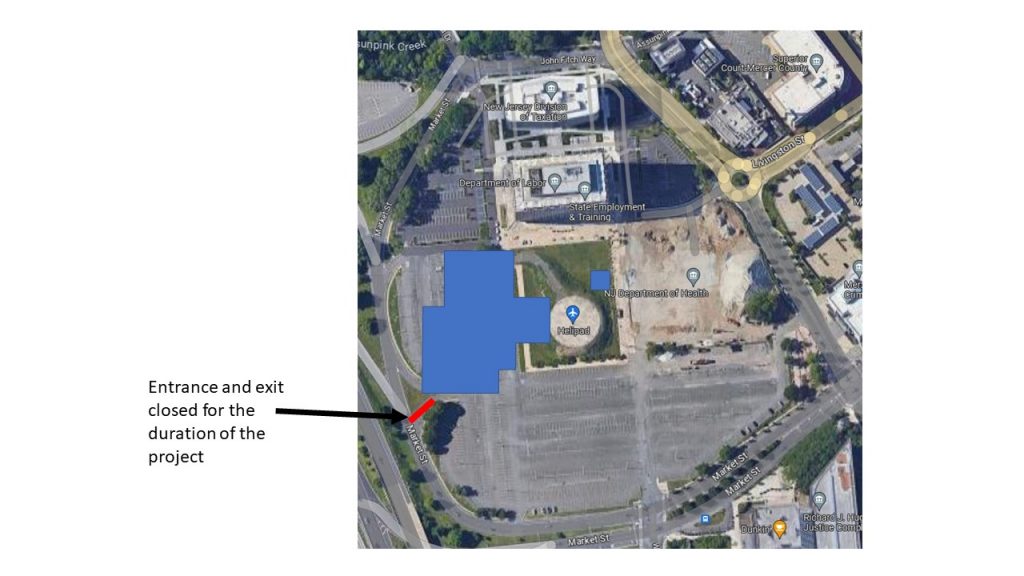
Q. What will the truck route be?
A. The final truck route can be found here.
Q. Was the planned maintenance on Route 29 and any other proposed roadwork factored into the decision on the final truck routes?
A. Yes. The final truck routes were determined by the contractor who will be shipping materials and wastes to and from the site and reviewed by the state and city police. The use of the Route 29 onramp is approved by NJ Department of Transportation.
SITE RESTORATION
Q. When the remediation project has been completed, will the state parking lot be restored?
A. PSE&G will follow the state’s direction regarding the size of the parking spots. Restoration of the work area will return it to its current condition as a parking lot.
UPDATING EMPLOYEES AND THE COMMUNITY
Q. At what frequency will updates on the project be available?
A. Updates are posted to the website and sent via email weekly.
If you have questions or concerns about the project, please contact us by the Project Information Line at (855) 356-2383 (TTY callers please use 711) or by email at comments@jfitchwayproject.com (right click to copy link into your email).
Please note the Project Information Line is automated. You will be prompted to leave your name, contact information and the reason for your call. One of PSE&G’s community liaisons will return your call as soon as possible.